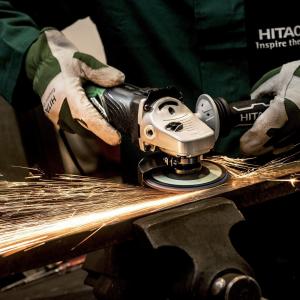
Metal fabrication processes, including milling, drilling, laser cutting, welding and so on, create a high volume of waste materials that can be dangerous to the environment. The two prominent wastes produced by this process are scrap metal and machining fluids. As regulations become stricter, these wastes can be dealt with by fabricators in various ways to achieve cleaner metal fabricating operations.
#1. Decreasing amount of scrap metal
Metal parts are cut out from the metal blanks in varying shapes and sizes. Most often than not, what remains is the metal scrap which is the largest waste produced by metal work processes. This scrap can be sold to scrap dealers or back to the metal supplier. However a much better way to minimize waste of metal scrap is to choose stocks or blanks that are closely specific to part specification. Fabrication shops can also work closely with the supplier in a manner that makes cutting occurs less often or when necessary.
#2. Preventing or eliminating the use of lubricants
Lubricants, also known as machining fluids, are used to enhance tool performance and life, improve the finish of the metal surface, and minimize workpiece thermal deformation. Most metal fabrication processes use either oil-based or synthetic lubricants. The best way to address the waste of lubricants is through dry machining. This process reduces the need to manage lubricant issues. Also, fluids can be greatly reduced with the modernization and optimization of equipment. Best of all, they can be eliminated with the use of new cutting technologies and systems.
#3. Reusing lubricants
Used machining fluids do pose health and environmental hazards and can be contaminated with swarf, which are fine chips or filings of stone, metal, or other material produced during metal work. These fluids can be recycled by removing the swarf through various ways such as filtration, centrifuges and hydrocyclones. Centrifuge removes oil-based lubricants from swarf, while hydrocyclones separate very fine particles from water-based lubricants. Other alternative ways include adding solutions that break up the waste lubricants for better removal of the swarf.
If your business is looking for a metal fabrication service provider that is forward thinking, using only the latest technology and processes then contact us at 4 Way Metal today to see how we can assist you.
